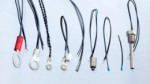
Thermistors vs. Thermocouples
Temperature sensors are important for everyday life, from working in industrial plants to preventing fires. Thermistors and thermocouples are two such temperature sensors.
A thermistor is a thermally sensitive resistor that exhibits a continuous, small, incremental change in resistance correlated to temperature variations. Thermocouples reflect proportional changes in temperature through the varying voltage created between two dissimilar metals electrically bonded together. Both are good options for temperature sensing and control. Choosing the best option depends on the type and specifications of the application.
When comparing any temperature sensor, there are four factors to consider:
- Temperature Range
- Stability
- Accuracy
- Application
Four Factors to Consider when Choosing Between a thermistor and thermocouple as a Temperature Sensor
Temperature Range:
NTC thermistors and thermocouples both operate within a wide range of temperatures, making them both ideal for a wide range of applications. NTC thermistors perform well in an operating range between -50 to 250 °C while thermocouples operate within the widest temperature range from -200 °C to 1750 °C.
Stability:
Applications with a long-term operation goal require stability. Temperature sensors can drift over time, depending on their materials, construction, and packaging. For example, epoxy coated NTC thermistors can experience a drift of about 0.2 °C per year; whereas, hermetically sealed NTC thermistors experience a much smaller drift of about 0.02 °C per year. On the other hand, Thermocouples experience a drift of about 1-2 °C per year, largely due to chemical changes in the sensor, such as chemical oxidation.
Accuracy:
NTC thermistors are highly accurate through incremental changes within their operating range. Small temperature changes reflect accurately due to large changes in resistance per °C. Thermocouples have lower accuracy and require a conversion of millivolts to temperature when used for temperature control and compensation.
Application:
Both NTC thermistors and thermocouples can operate within a wide range of applications; however, NTC thermistors are commonly found in life safety applications like fire detectors and thermometers because they are accurate and stable. Thermocouples are more often used in industrial settings due to their durability and cheaper production costs.
NTC (negative temperature coefficient) Thermistors
An NTC thermistor is a temperature-sensing device made of sintered semiconductor material that contains a mix of several metal oxides. These materials possess charge carriers that allow current to flow through the thermistor, displaying incremental changes in resistance proportional to temperature changes.
NTC thermistors produce higher resistance at lower temperatures. As temperature increases, the resistance of the thermistor decreases. Since thermistors experience such a large change in resistance per °C, the smallest temperature change is expressed rapidly as a predictable change in resistance.
Locating the right thermistor for an application requires calculating the resistance versus temperature using the thermistor beta (β) formula. This method uses a two-point calibration to calculate the resistance versus the temperature curve, and it calibrates the resistance at both temperature points.
The output of an NTC thermistor is non-linear due to its exponential nature but can be linearized depending on the application.
NTC Thermistor Applications
NTC thermistor temperature sensors are available in various sizes and styles, such as customizable probe assemblies, glass encapsulated, surface mount, and disc and chip styles. These attributes make them adaptable to perform well in many industries such as automotive, aerospace, medical, and HVAC.
Though many applications that use NTC thermistors focus on resistance versus temperature characteristics, thermistors also fill a need in other electrical applications such as Current-Time and Voltage-Current characteristics.
Current-Time can include:
- Time Delay
- Surge Suppression
- Sequential Switching
Voltage-Current can include:
- Fluid Velocity
- Liquid Level Control
- Voltage Regulation
- Temperature Control Circuits
If a higher accuracy rate is in order, you can use NTC thermistors in conjunction with a Wheatstone Bridge. This circuit acts as a comparator, where small temperature changes can be accurately reflected.
Thermocouples
A thermocouple is constructed using two wires of dissimilar conducting metals electrically bonded at two points. Together, they form two electrical junctions; the measuring (hot) junction and the reference (cold) junction. When those junctions express different temperatures, they produce a milliampere DC voltage or thermo-electric voltage. Thermo-electric voltage is then translated into temperature in the temperature reading instrument.
Referenced in this article is the “K” type. This thermocouple operates over a broad range of temperatures ranging from -200°C up to 1250 °C. Furthermore, because of the metals used, it is one of the least expensive thermocouples; however, thermocouples have reduced accuracy and are susceptible to calibration drift over time.
Figure 1: Example K-Type Thermocouple Standard Configuration
Thermocouple Applications
Thermocouples are primarily used in industrial settings because they perform best in extreme temperatures. Steel and Iron industries use thermocouples to measure and control temperatures in furnaces, kilns, and boilers.
A thermocouple’s lifespan is hard to predict. One method to predict their stability is to install the thermocouple and evaluate its performance to determine its estimated lifespan.
Thermocouples function well in a wide range of environments, but oxidation can cause the “Green Rot” phenomenon. The chrome alloy in the thermocouple will turn green after being exposed to a reducing gas, such as hydrogen, during contact with the metal wires. This oxidation reduces the voltage and causes the thermocouple to produce a lower reading.
THERMISTOR VS THERMOCOUPLE : NUTS AND BOLTS COMPARISON
For use in Temperature Measurement and Temperature Control
Temperature Sensors: Thermistors vs ThermocouplesNTC thermistors weigh in to be an excellent choice for your temperature sensing solutions for their overall performance and cost-effectiveness. They provide:
To learn more about NTC thermistor temperature sensors and Ametherm, visit us at www.ametherm.com. |